New Production System
AN INTRODUCTION TO NEW PRODUCTION SYSTEM (N.P.S.)
Consequent to the recent GATT agreement on Trade between Nations a phenomenon
is occurring world wide for going towards globalization and the whole
world is becoming a Global Village. Because of this the industrial environment
is undergoing a transformation. The environment of “National Protection”
is yielding place to one of “Global Competition”. The industries have
to respond fast to this change and gear themselves up to operate and succeed
in a competitive climate. And again, this competition will not be only
from the domestic producers but on an international level as well. The
prime requirements to be met to succeed under the competitive climate
are :
- Speed to market, or faster response to customer needs.
- Continuing improvement in quality.
- Control on costs and cost reduction
Such a sudden change in demand of the operational environment calls
for a change in basic policies, procedures and work systems. Faced with
a similar competitive situation, the Japanese visualized and evolved a
very innovative system, the basic approach of which was to eliminate waste
in all spheres of activity, which took shape as “JUST IN TIME” or JIT
system of production. Progressively this new system came to be refined
and broad-based, and it crystallized into a system of production covering,
not exclusive elements like inventory, quality, cost reduction etc., but
the entire spectrum of production activity starting from the stage of
receipt of customer orders to dispatch of finished products. This system
is called the New Production System (NPC). The basic definition of NPS
is :
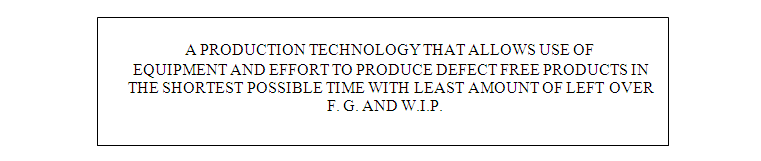
As would be seen from the definition, NPS strives to provide the means
to meet the demands made by the 3 features referred earlier, viz. Fast
Customer Response, Quality and Costs. And this is sought to be achieved
simultaneously with a system of Total Employee Involvement (TEI). TEI
is a major feature of NPS system and it is based on the premise that the
employees (operators) have abundant inherent talent and this talent is
to be harnessed for the benefit of the organization, and also the employees
themselves. The means to do this is to create through appropriate policies
and procedures an environment wherein the employees feel they are fully
involved in day-to-day problems of production, particularly in their respective
areas of operation, and inculcate a spirit of team-work.
Given the Total Employee Involvement as a common factor in all elements,
NPS is a system structured on individual operational elements like the
following :
- Manufacture against firm orders, and not to stock.
- Reduction of Manufacturing Cycle Time through
- Cellular System of Production.
- Small Lot Production.
- Pull System of Production..
- Quick Change Over.
- Total Quality Control.
- Total Productive Maintenance.
- Just In Time Purchasing.
- Focused Factories.
- House Keeping.
An interesting aspect of NPS is that dependent on local conditions any
one or more of these elements can be taken up for implementation to begin
with and then progressively extended to other fields.
Customer satisfaction is one of the key approaches under NPS. In order
to achieve this, great stress is laid on Quality factors like commitment
to quality through self-inspection, finding solutions to problems as and
when they arise, removal / remedying the root cause of the problem to
ensure it does not occur. In the current context, this features would
be of special significance to such organizations who are interested and
are planning to obtain ISO 9000 Certification.
QUICK CHANGE OVER (QCO):
AN INTRODUCTION :
Quick Change Over (QCO) is also known as Single Minute Exchange of Dies
(SMED). However, SMED suggests a rather limited application, we however
prefer to use the term QCO as being a more general & universal term
to describe this technique.
QCO is one fact of the revolutionary Japanese New Production System
(NPS). Earlier Authors referred to these techniques as Just In Time or
World Class Manufacturing (WCM).
Continuous improvements in manufacturing system, practices & processes
are necessary for any Organization to survive & prosper in a competitive
environment. Equally important is flexibility to effectively meet Customer’s
Demand. QCO is one important component of this effort.
For years now, companies have concentrated on increasing output &
reducing machine down time during scheduled operating hours. However,
little attention has been paid to the equally important need to reduce
the time taken for setups from one job to another. It is only in recent
times that attention has been paid to this hitherto neglected aspect of
machine down time & a formalized system incorporating these techniques
has been developed called QCO. Its achievements have been quite dramatic.
IN THIS WORKSHOP, WE WILL :
- Introduce you to the basic principles of this revolutionary technique.
- Help you understand the techniques by analyzing Indian case studies
in Indian Industries, here QCO has produced impressive results.
- Help you analyze your own manufacturing procedures & practices,
so that you can uncover areas which can benefit from the introduction
of QCO.
- Create an awareness that QCO actually works!
QCO : IMPLICATIONS & BENEFITS – QCO MEANS :
- More frequent changes in production schedule.
- Running Smaller batches.
- Shorter production cycle time. Hence lower response time.
- Lower inventory & WIP. Hence faster capital turn around.
- Higher Manufacturing Velocity Ratio.
- Higher Inventory Turns.
- More flexibility; Faster response to demand changes.
- Mixed Production possible.
- Simplified Setup.
- Setups can be performed by unskilled workers.
- Small Group Activity. Worker is owner of decisions.
- Less effort required during setups by the worker.
- Less monotony, greater opportunity & challenges to a worker.
- Workers Efforts Recognized.
- Better Quality.
- Less waste . More time is available for production.
All this means :
- Better competitive strength for the company.
- Better employee job satisfaction and, consequently, morale.
GUIDELINES FOR QCO :
- QCO calls for a team approach. Form a task force comprising of
personnel from all concerned sections. Do not omit to include setters
& operators.
- Do not leave problems of set-up times to be resolved on the shop
floor. These have to receive proper attention from the Task-force.
- QCO requires set-up operations to be observed, recorded & analyzed,
preferably on Video, if significant reductions in set-up time are
to be achieved.
- Make check-lists of all items required for the set-up, including
the tools, as also all the steps involved in the set-up; this is like
a process, sheet for a production job.
- Provide each set-up Team with a complete tool kit. To go to the
tool-crib to draw a tool or go round to borrow on mid-way during a
set-up is an avoidable waste of time
- Store the tools at its allotted place near the point of use, in
a ready to use condition.
- Check & ensure availability of all hard-ware items like bolts,
nuts, washers, shims, clamps, hand tools, etc. well in advance while
the current job is still running.
- Eliminate the waste searching. Use shadow boards where possible.
QCO TECHNIQUES :
- Use – U shaper washer.
- Use U-shaped slots on dies, jigs, fixtures, etc. in place of drilled
holes.
- Use pear shaped holes for clamping. Do not remove nut from bolt;
loosen 1 or 2 turns only, slide 7 remove job. Searching for a bolt
is eliminated.
- Use bolts of correct size. Longer bolts waste time screwing &
unscrewing.
- Reduce number of bolts used for clamping to the bare minimum.
- For fastening work piece to the machine, use 2 washers with a drop
of oil between the two. The work piece will then not move when tightening,
eliminating the need for resetting.
- Use quick acting clamping devices.
- Standardize clamping heights of dies.
- Functionally standardize all tools & dies.
- Use Cassette System like in a tape recorder.
- Have roller conveyor carts / trolleys of same height as machine
bed for transporting dies.
- Where feasible, store dies around the machine on roller conveyor
tables.
- Incorporate “Click” to align principle. Eliminate adjustment totally.
- Use Intermediate Jigs.
- Change lathe tips outside the machine.
- Where feasible, adopt parallel operations.
- Preheat dies in injection-including die-casting operations this
saves time.
- Utilize the heat dissipated from the current operation to pre-heat
the die for the next job.
- Where Assembly lines require layout changes, provide work tables
with caster wheels.
QCO : HOUSE-KEEPING :
- Simplification : Keep only what is necessary on the shop-floor.
- Organization : Designate locations for every tool, gauge, part,
material, etc.
- Discipline : Keep every thing in its designated location.
- Cleanliness : Clean everything immediately, to be constantly ready.
- Participation : Everybody cleans their own areas & observes
Housekeeping rules.
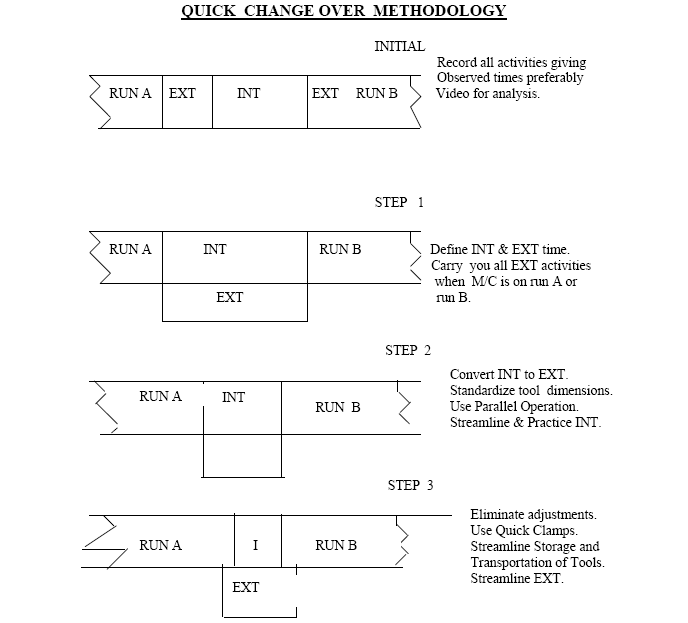